How Ford’s Technical Specialists Manage a Globalized Workforce
The automotive industry is in a state of rapid change. In addition to the expedient move to electrification, auto manufacturers around the world are becoming increasingly global. Not only are more auto manufacturers selling cars around the world – many are also leaning into a global workforce to make vehicle concepts and updates a reality for consumers.
Ford has long been at the forefront of the auto industry and remains near the cutting edge of electrification. The auto mainstay has also adapted to a globalized workforce, employing people outside of its traditional Dearborn, Michigan headquarters to help it produce vehicles.
Steve Frank, Body Structures Technical Specialist at Ford knows more than anyone how much the auto industry has changed, particularly within Ford’s walls. He’s been with the company for over 25 years and has worked on Body Structures his entire career, which includes 4 generations of Mustangs and vehicles like the Thunderbird, Escape, Edge, and several exciting future model products. He now leads a global Body Structures team encompassing “essentially anything that’s metal on the outside of a car that you would see.” Steve walks us through what his day-to-day is like in 2024, giving a rare glimpse into how Ford is continuing to lead the way for the auto industry.
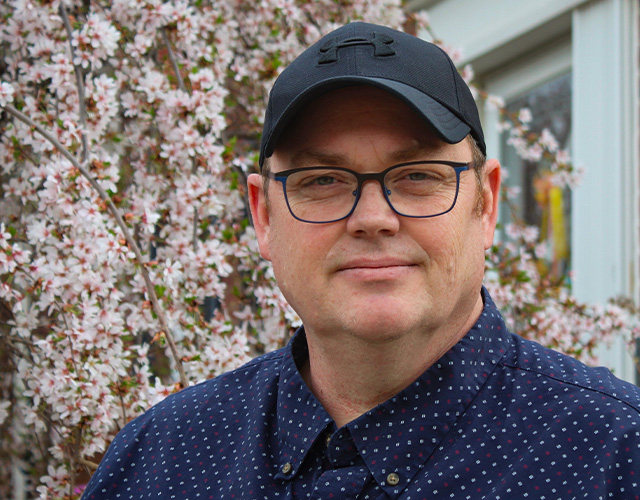
Steve Frank, Body Structures Technical Specialist at Ford
What’s the scope of your work?
I am one of four global Technical Specialists who are responsible for the Body Structures Subsystem technical execution across North America, Europe, Asia Pacific (including China), India and South America. My role is to help technical execution through my Standards: Design Rules, Requirements Test Methods, and Engineering Specifications.
I guide each program team’s design utilizing these standards to meet global and regional regulations as well as Ford’s internal requirements. I assess those designs during the early development of a program and provide guidance/direction to the teams based on my experience and lessons learned. I review each of these programs and audit designs at critical milestones to ensure they are aligned with the program’s deliverables. I will also provide technical improvement suggestions and feedback, helping to avoid production issues and late product changes.
What’s a typical day for you as a technical specialist at Ford?
It’s funny, because my day is not my own. When I start my day, I have a plan of action and a laundry list of items that I want to work on. But by the time I get my first coffee, my plan is already out the window. Since I’m a global Technical Specialist, by the time I start my day, Asia Pacific’s (Including China) Program’s Body Structure team has already begun reaching out to me. That continues throughout my day as the European Program teams begin to complete their day around noon in Dearborn, Michigan. Then the Dearborn-based teams, as well as the South American and Mexico-based program teams, round out the end of my day with questions.
This relationship helps those teams have a core view while getting feedback and lessons learned from other regions through me. I gain valuable feedback as well, and I get different points of view on how each region understands my requirements. As a Technical Specialist, I am the acting Global Technical Hub of Information while learning about how other regions develop more engineering and cost-effective design solutions.
What are some of the challenges of working with a global team?
A lot of times my job is a ‘jack of all trades.’ I get questions that can be broad around Ford Processes or very specific in nature about a particular technology. As a Technical Specialist, it's about having a teammate to whom you can go to ask quick technical questions without repercussions. These discussions tend to be light-hearted and open, but that open discussion leads to deep and thoughtful questions in future discussions. We also have engineers that have joined the team who have recently graduated or are entry level/junior engineers. I am here to help those that are new get an introduction to Body Structures. And for the more experienced team members, I provide that technical shadow, guide, or mentoring for how to address the problem.
It took time for me to realize that I am a resource and not an answer for those regions who are reaching out. I need to be like a good librarian. These regions don’t need someone to ‘find the book for them’ but to provide insight on how to look at the book. It’s about ‘how’ to find the answer and not about ‘what’ the answer is.
Are you seeing more turnover, more entry level and junior engineers within the company?
It’s accelerated in the past few years. Prior to COVID, we were starting to see it more frequently, and I think the pandemic made turnover a more regular occurrence as engineers look to work from home. When I started to see [turnover] was when Original Equipment Manufacturers (OEMs) moved away from traditional pension plans. Migration between companies started to increase as engineers looked for better pay and benefits.
The specialization we used to have was replaced by a mindset of being nimble and efficient and adopting a start-up mentality. Ford embraces that mindset as we continue to evolve our corporate behavior away from the large organizational structure that is modern. Having a wide range of knowledge and training in the company is a healthy way to encourage questions and growth. So, if we want to innovate and be a leader in engineering we can’t do that without knowing the limits of the design. This means failing in testing in order to provide a successful product. We have internal processes that protect the product before the design is released. Designing to the status quo will only produce a vehicle structure similar to vehicles made over the last 10-15 years. Ford wants to lead in engineering for the next 10-15 years.
So, turnover may be higher, but Ford always tries to retain those who have that start-up mindset.
What’s the training or experience they’re looking for? What are you able to provide that sets them up for a better career?
Ford looks to hire engineers that can communicate their vision in the most efficient way possible. For engineers that may be in PowerPoint or Excel, but we find that its most efficiently communicated via CAD. Visual representation is the best way to communicate with regions where English is not their first language. I work with lots of smart engineers with very diverse backgrounds and different viewpoints. I am a very hands-on, ‘roll up the sleeves’ type of person and am great at communicating my concepts via drawing and sketches.
When I first started, my mentors and supervisors allowed me to make mistakes. They allowed me to learn through testing but never allowed a bad design to be put into production. I remember my mentor telling me once, ‘It’s better to fail in the lab through testing than it is to fail in the field on a customer unit.’ That taught me not to be afraid to jump in with both feet to learn during the development process.
My personal goal is to keep each problem simple because, as engineers, we can make it difficult and complex. Other team members may be more detail-oriented and can see detailed opportunities. This is why Ford celebrates diversity in people and thought, so when we bring in all these different viewpoints, it brings different ways of thinking. Together, we are rewarded with an efficient and robust design solution.
How has your role changed in the past five to seven years? What platforms and tools do you use to get the job done?
We’ve migrated away from PowerPoint presentations and going up through the management chain. These days we have reviews at our internal requirements database and go over the analytics of the data in real-time. We are more likely to look at CAD, CAE, 3D Prints, or Low Fidelity mock-ups with the VP of Engineering. It’s now less about presenting and more about data. It’s about quick decisions rather than compiling an outstanding presentation.
Why do you think ‘presenting less and doing more’ is important now?
As soon as you make any presentation, it’s only as good as the data you add at the time. Data flows much faster through the organization now. It would take days or weeks to make a presentation, and by the time you’re done, the data may have changed. We work in a global environment where many of our CAD/CAE resources and many of our team members are also in different regions, and they’re working at times I’m not in the office. So, I can come in and see CAD data has been updated overnight (for me). Because of that, creating a presentation adds to the workload and time, whereas now I can review a CAD/CAE and make real-time adjustments, suggestions, and changes. I think management understands working in real-time makes a big difference in the quality of the program decisions.
How has remote work and a global workforce changed your workflow?
The Program Teams I work with and guide are much more global now in areas throughout the United States, Brazil, Germany, India, China, and Mexico. They are not always in the Design Centers. They may not be at the location they are designing the vehicle for. Assembly plants are also global in nature, now. We have many assembly plants dedicated to specific models, too. The Engineering Team must be knowledgeable of all regional regulations and requirements - or at least know where to find the information.
We have learned to evolve and communicate differently from the ‘old’ ways. Working globally, you cannot simply walk to someone's desk anymore, but we have found a quick video chat or screen share is just as effective.
When the pandemic hit, Ford found it was not as ‘business altering’ as we were already working virtually across teams. Engineering support functions like CAD and CAE in other regions allow the engineering teams to focus on the data driven decision and resolution. After a decision is made, direction can be provided to teams in places like India or Mexico. When direction is given at the end of the day, CAD or CAE updates are available when teams start the following day.
Does that mean you’re qualifying their work for production?
As a technical specialist, I audit designs before release. We also stress the importance of peer evaluations. These evaluations are an important element to ensuring we are efficient in our designs and processes. No one person is responsible for design; it’s a team effort spanning many subject matter experts and technical specialists, and a late change due to Testing Failures or mass production/manufacturing issues is detrimental to the product.
Each design, surface, gage, and coating are thoughtful and rationally selected for each region. Some regions have more stringent crash requirements. Other regions may be more critical about replacement parts. So, we might have to change designs to make it more efficient for one region over another. We review data and make data-driven decisions as a team. I also review data accuracy to ensure we have testing and evaluations for product launches.
How has the move towards electrification changed workflows?
Our team’s role has changed a bit with electrification. Our goal is to meet crash requirements while efficiently leveraging any structural systems as we can. This means evolving design strategies to include the body structure, battery structure, and the frames/subframes. EVs have more mass and are heavier, so there’s more force potentially hitting a vehicle.
We have to be efficient about how we use designs and manage that load. Inefficiency in weight can impact a vehicle’s performance. We want to keep structures mass low as it will impact the overall force that we must withstand ultimately meeting our crash requirements.
What is your biggest challenge with managing so many teams and signing off on designs from a globalized workforce?
Different regions may have a unique understanding of what’s being communicated in our requirements. English may not be a region’s primary language; metaphors may not be completely understood in non-US regions. We may also be saying the same thing but understanding it differently.
I’ve found that communicating through drawings and sketches helps tremendously. It’s almost like art is a second language. We can see in these meetings when it ‘clicks,’ and they understand the sketch or the concept. This generates additional discussion and engagement. It’s not just about communication via CAD, it’s about communicating a thought and getting feedback.
Let’s say Ford is bringing in a new technical specialist – a peer for you. What’s something you’d suggest they do to be successful?
When someone new joins my team, I encourage them to go break something. Too often, we design to a lower limit, and we don’t know what the upper limit is. I want to understand both sides of that equation. I want to know when it fails, and is successful. Failure is a good teaching resource. You don’t learn anything until you fail.
I’m also a proponent of experiencing things. When engineers test their design and participate in the hands-on evaluation, they are exponentially more likely to remember it and thus build from it. Experiencing things firsthand is a wonderful way to learn. So, we are all engineers. Get out there, break something, and learn how to make it better!
View our Dice Company Profile to learn more about open tech positions at Ford Motor Company
Additional articles and insights from the Ford team can be found here.