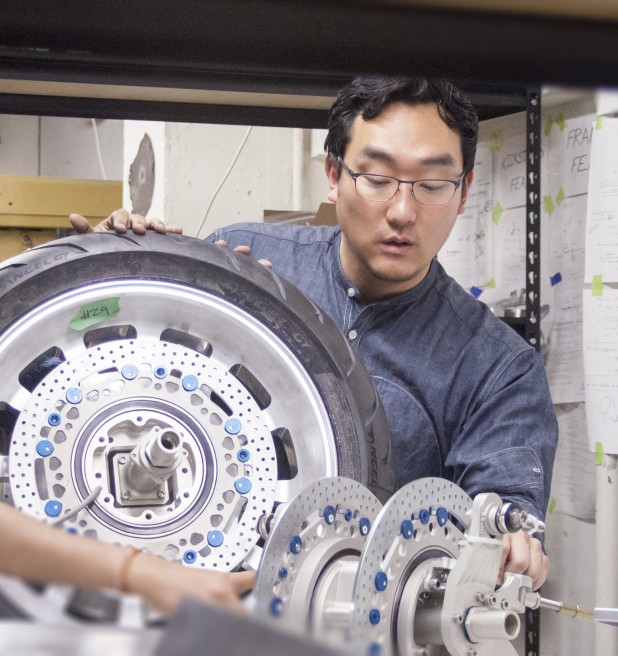
In early March,
Lit Motors founder Danny Kim hit the road to meet investors. The Portland native needed to keep the momentum growing for his small firm, which builds the two-wheeled
C-1. His modest lab, located in San Francisco’s SoMa neighborhood, could accommodate another 12 employees—but he needed the money to fund them, and to build a manufacturing facility capable of turning his prototype ideas into a reality. Like Elon Musk and other manufacturing
savants, Kim is someone who enjoys the challenge of building things—whether it’s eyeglasses, chairs, or motor vehicles from scratch. He’s spent the past five years re-thinking modern transportation, and using those insights to design prototypes of two-wheeled, motor-driven vehicles that can self-balance with a dancer’s grace, thanks to an integrated software platform and a patented gyroscopic system. Even as he traveled to New York to raise funds, Kim’s heart was back in San Francisco, and the three-story workshop that serves as a sort of DIY museum to his ambitions. Part of the space includes a storefront for the C-1, which (if everything goes well) will begin mass production at the end of this year. The attached shop features lots of space for engineers and designers to collaborate over their plans to change how people get around, especially in urban settings. [caption id="attachment_18243" align="aligncenter" width="618"]
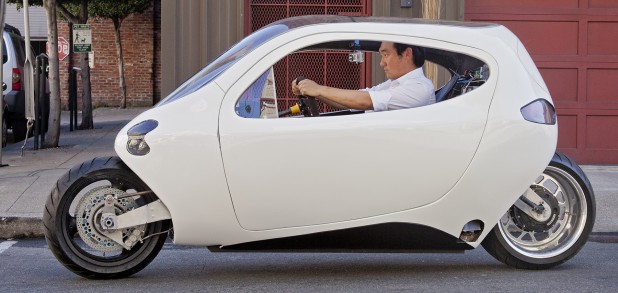
The C1.[/caption] In a wide-ranging conversation, Kim discussed his plans for manufacturing the C-1, as well as the challenges in convincing consumers to try out a new kind of vehicle.
Q: How did you develop an instinct for design? Do you think this is something that comes naturally to you, given the way you perceive the world? Danny Kim: After I dropped out of Reed College, studying physics and biology, I was interested in how to invent things. There’s a path to design and there's a path to engineering. I started developing my own philosophy of design and engineering, where they drive each other in a simultaneous process. I think that's what got me interested to go to Rhode Island School of Design to get a degree in Industrial Design and Sustainable Transportation. When you are designing a car, it's hard to hire 10 separate people [to work on the design and the engineering and expect it all to line up]. What I've been able to do is combine those roles by being the architect, while leading the transportation design, and acting as the mechanical designer. This way, I can come up with a reasonable solution to any problems that arise. I'm the intersection between design and engineering, and that's why we can get so much done so quickly and cheaply. Engineers are interested in the details, and then rarely can zoom out into high-level discussions on how to integrate electrical wiring to code to dynamics and mechanical systems.
Q: You talk a lot about engineering. But I want to know more about how you think about design. DK: Besides the technical aspects of vehicle design, how do you create a product that feels amazing? How do you make a product with natural and intuitive human experience? That's where design sets in. It ensures that products’ exterior, interior, and experience evokes an emotional relationship with of the driver/user. I have these conversations in my head: What does the exterior need to look like? How does the UX make you feel? Are we within the confines of the
H-point? To support that with the engineering and have a robust platform, I manage or lead all those fronts. I could not have done that without the previous experience I had. I dropped out of college, traveled the world, worked as a Land Rover mechanic and built two custom SUVs from the ground up and went to design school. There's no real education or academic track of how to start your own car company, you just have to do it.
Q: Why did you drop out of Reed College? DK: It was a pretty academically rigid institution... it was really fun. You go there to get a PhD, or become a lawyer or professor. It didn't fit me really well. I learned quite a bit. I told my parents that I was doing the Steve Jobs thing by dropping out. My parents said: "What, who is Steve Jobs?"
Q: How did you settle on a 2-wheeled vehicle as the way you want to solve the transportation problem? DK: Well, 72 percent of commuters drive alone, so it just made sense to cut the car in half. You have to think about this two-wheeled car as a robot because of its stability. It purely uses our AI/stability algorithm so it can balance and you don't have to. We had to develop our own firmware for our own dynamic system. It is code heavy. We have four people writing the firmware on it for the last four months. It's relatively complex; it's not something you can hack. I’m thinking about opening it up to Android so someone could create their own skin for the interface or design the interior display. Right now, however, it's our own platform that uses ARM processors. It would be easy to open it up to Android.
Q: What made you think about transportation as the thing you want to devote your life to? DK: I had an accident that almost killed me when I was rebuilding one of the two Land Rover Range Rovers. It made me ask myself, why am I building big SUVs? It's more efficient to build a motorcycle. I began to ask questions such as, why don't people use motorcycles more? It's inconvenient because of rain. But it is dangerous on the highway. Why couldn't you have something in between a car and a motorcycle? Why don't we just cut the car in half? Could it be a two-wheeled car? It's impossible to keep a fully enclosed motorcycle in balance. It makes sense to put a gyroscope in the vehicle. I did a quick calculation to see if it would make sense to have a gyroscope in a bicycle. So it made sense to do it in a motorcycle too. I wrote a provisional patent, and signed up to attend Rhode Island School of Design to learn how to build a product and manage engineers.
Q: From when you started Lit Motors to now, how has your philosophy about design and engineering changed? DK: My philosophy hasn't changed too much. It has been substantiated with other technologist and validated with adjacent industries. We need a sustainable vehicle. The field of robotics is becoming more commonplace for aspiring entrepreneurs. Sustainable vehicles are the future and if you can make it affordable and safe you have a recipe for the Model T of the 21st century.
Q: What’s practically necessary when thinking about mass producing a vehicle? DK: We established a production process: a sequence of assembly and bill of materials: two things that are essential to producing anything. You have to know what your sequence of assembly is and your bill of materials. Besides your supply chain and having an actual factory, there are the four big things that you have to worry about. Some people call them the four Ps: Product, Process. Plant. People. I've been working on those four Ps… the last one we don't have: people. I'm looking for a manufacturing plant. We have our product. The product is going to get better over time. We are on prototype number four-and-a-half. We are building an awesome team of diverse skill sets. I'm a pretty hands-on type, I learn and synthesize predominantly through the empirical processes. Sometimes the best thing to do is to just do it. It's hardware, so you need all hands-on deck, the ability to iterate quickly, learn on the fly, and have a peer review. I ask smart people who have 10-20 years experience or so, and have been able to learn a lot from them.
Q: How do you know if you should actually listen to their advice? DK: I have been compiling a rather large dataset of advice; I can usually tell when someone is [expletive] me. I know a lot of people who have done production for larger runs. Depending on scale, there's a pretty consistent language and processes involved and a level of concern of which to mitigate failure. You are going to be making mistakes. The difference between a smart founder and one that isn’t is, the smart founder when making a complex decision might pick a somewhat logical direction without all the correct information, moving the company forward. Carefully monitoring the progress and change directions quickly if needed to mitigate the damage. It is about staying on your toes, and I have been doing that somewhat well over the last four years on a really small budget. We’ve raised $2.2 million, with almost $1 million in pre-earned sales of our first production run (around 890 pre-orders). It cost half a million dollars to build a high-speed prototype. That will be something that we will have finished over the next few months. Right now, we have 5 patents that have been granted. Our team has grown from 6 to 18 people. We are very well poised to get further funding and go into production.
Q: Are you working hard? DK: Yes, I work 14-hour days and usually work until I go to sleep. We are developing a rather large product so it takes time to build. Regardless, you have to put in the time to make it happen; my entire team knows this. We are here to make change and eventually make some money in the process.
Images: Lit Motors